Use case: Sensor skin for wind turbine condition monitoring – energy self-sufficient eologix sensors are mounted directly on the rotor blade surface. (Copyright: eologix sensor technology gmbh)
Click to start the video
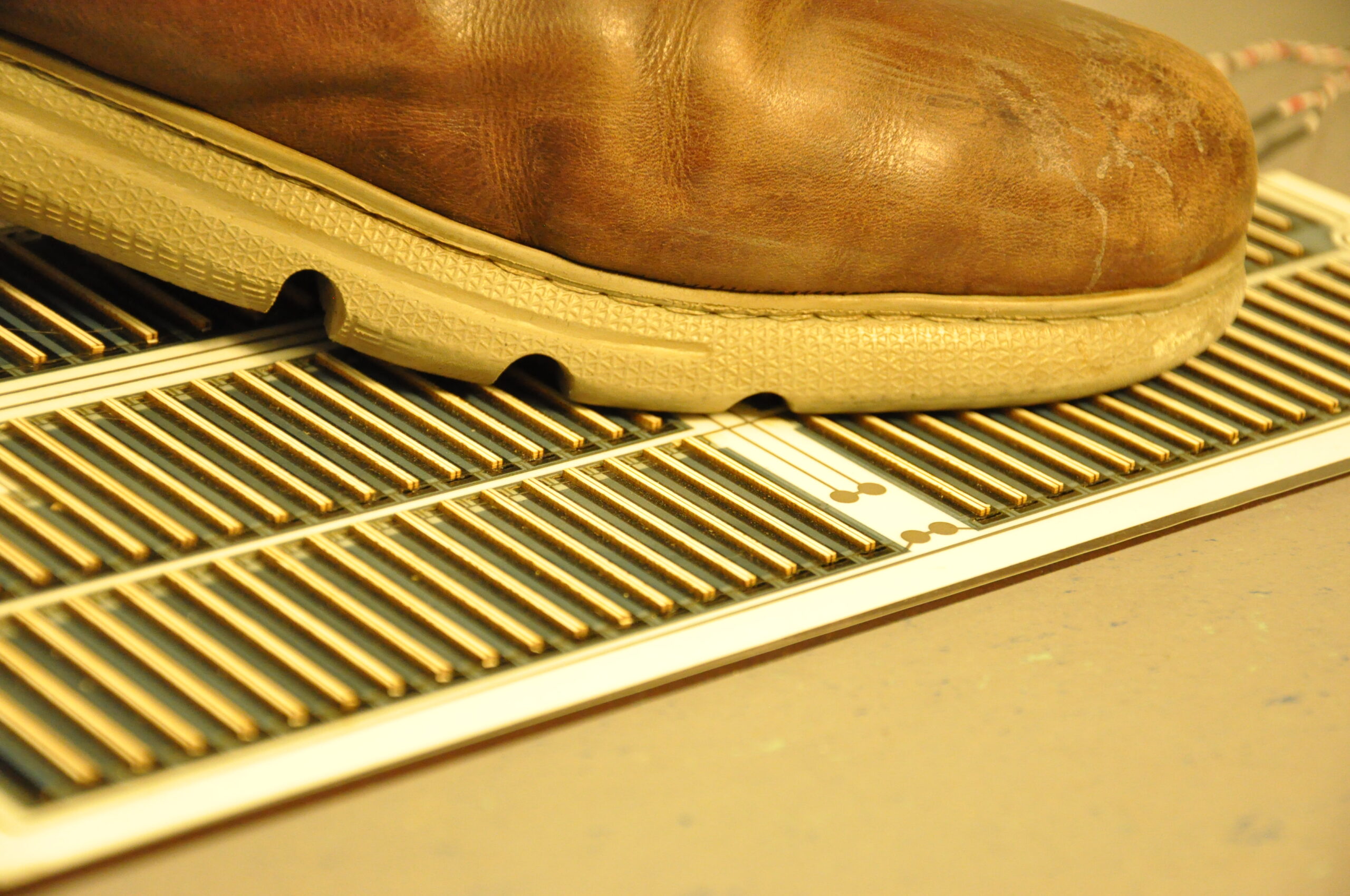
Use case: Smart floor. (Copyright: Joanneum Research – MATERIALS)
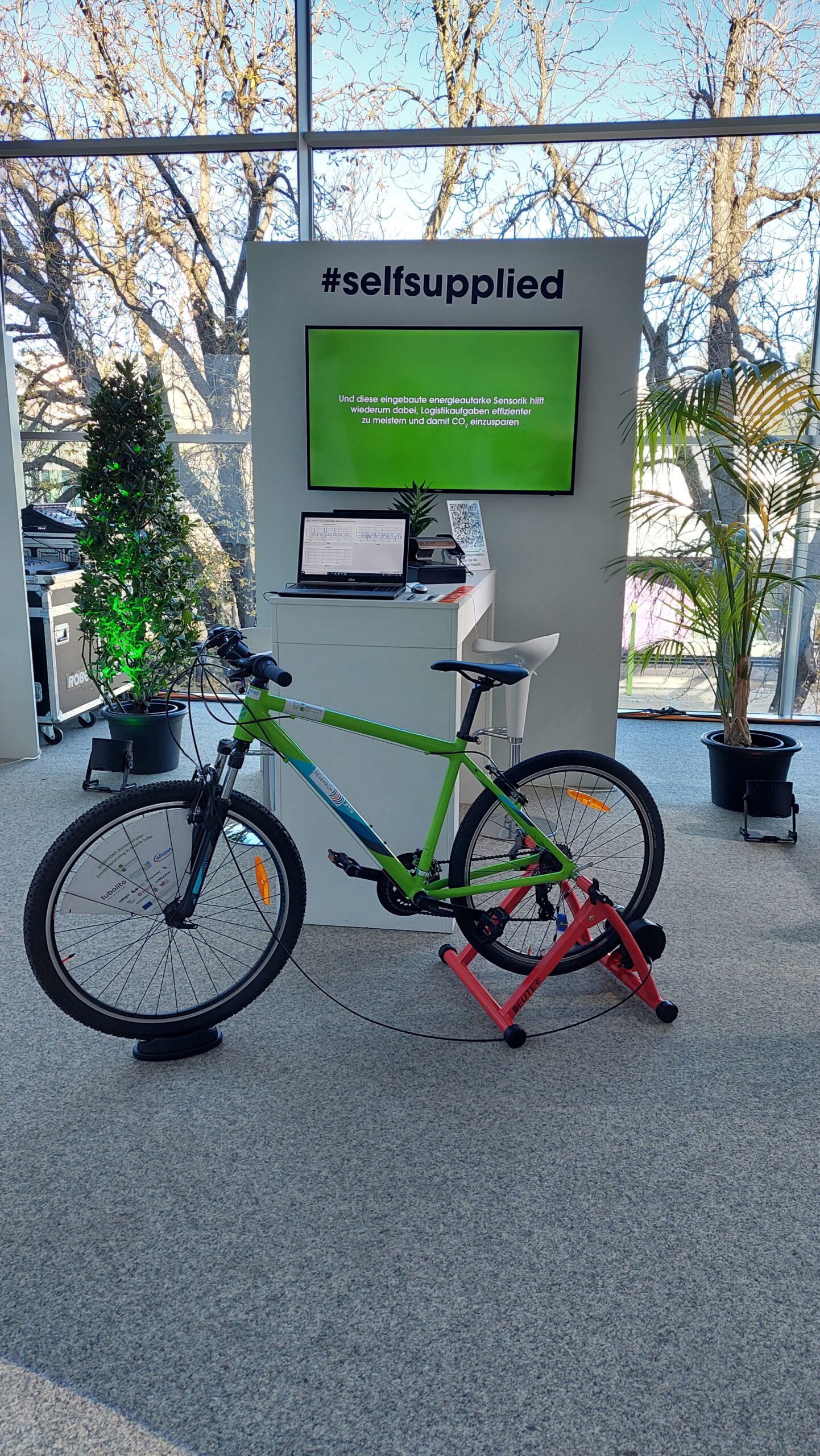
Use case: Automated pressure monitoring of bike tubes.
(Copyright: Markus Frühmann, Tubolito Gmbh)
Application Areas & Application Opportunities
SYMPHONY adresses three use cases to validate the impact of its new energy harvestig materials: wind turbines, bicycle tubes and smart floors.
The project will develop an integrated sensor skin based on the SYMPHONY Energy Supply Platform and P(VDF-TrFE) sensors that allow Condition Monitoring of rotor blades of wind turbines to increase their lifetime and reduce downtimes.
An automatic remote monitoring of the pressure of bike tubes will help to keep it, will reduce the maintenance costs for rental e-bike systems and will overall decrease the electrical energy consumption.
The wind turbine use case in detail:
Ice accumulation on wind turbine rotor blades has a crucial impact on operation and maintenance. Lower return due to aerodynamic imbalances as well as safety of the power plant and its surroundings are of central importance.
eologix’ retrofittable sensor systems for early and exact detection of ice build-up are based on wireless, flexible, smart and energy-self-sufficient sensors. These devices are installed directly on the surface of rotor blades.
Operation and maintenance of rotor blades amounts to up to 20 % of the OPEX costs of a wind turbine and are therefore one of the highest cost drivers. The outer third of the blade is responsible for the largest share of energy generation and is also exposed to the highest forces (wind speed, temperature, bending etc.). For this reason, eologix developed the first sensors that can be mounted directly on the entire surface of the rotor blade, which are enabling condition monitoring in real time and during any operational state of the system.
eologix aims to further enhance blade optimization by means of innovative sensor technology. Therefore, the sensor system is continuously further developed to provide even more relevant condition monitoring data from the blade surface.
Numerous pilot projects are currently being carried out in this area. eologix plans to start comprehensive commercialization of further applications in 2021 and the following years. The technology developed in SYMPHONY will be a key component for an even further enhanced system after a successful collaborative project.
The smart floor use case in detail:
The room heating, ventilation and cooling in private and public buildings accounts for 50% of the energy consumption in the EU. The intelligent control of home technology based on the actual usage has been evaluated in different use case studies, showing the high potential for energy savings [1,2]. This is especially relevant in existing, poorly insulated buildings. Existing technologies for occupancy recognition, based on optical sensors or cameras have disadvantages related to privacy concerns, high installation costs and the sophisticated data interpretation.
The harvesting and sensing technology based on printed piezoelectric polymers that will be developed in the SYMPHONY project, can be easily integrated into floor panels and power the readout and data transmission. This enables precise, high-resolution motion tracking to be carried out without endangering the customer’s privacy or requiring additional installation steps. The SYMPHONY self-powered solution will replace batteries and lead based energy harvesters, avoiding toxic waste, through the use of resource efficient and large scale production technologies.
[1] Press release: Forschungsprojekt: Energieersparnis durch Smart Home-Systeme, https://www.thkoeln.de/mam/downloads/deutsch/hochschule/aktuell/pm/2018/pm_17_smart_home_rosrath.pdf, accessed on the 16.08.2019
[2] T. A. Nguyen, and M. Aiello, Energy intelligent buildings based on user activity: A survey. Energy and Buildings 56, 244 (2013).
The remote pressure monitoring of bike tubes use case in detail:
Bicycle tire pressure directly affects rolling resistance, ride comfort, puncture protection, and grip. In e-biking (typically 3-5 bar), rolling resistance also affects battery life. In triathlons (typically 8 bar), rolling resistance is a winning factor. In mountain biking, grip is strongly influenced by pressure (typically 1.5-2 bar). For all 3 examples, bikers must measure the pressure before riding – as simple as possible. A wireless tire pressure sensor mounted in the tire tubes could improve driving experience and comfort as well.
For all use cases, monitoring tire pressure can also prevent serious injuries, as we also know from the automotive industry. In the automotive industry, tire pressure monitoring is required by law.
Tubolito uses a special thermoplastic elastomer called TPU, which makes Tubolito tubes not only significantly lighter, but also more robust (according to needle penetration lab tests) than standard butyl rubber tubes. Tubolito offers a complete range of tube sizes for most types and styles of bikes on the market. As a result, Tubolito has a deep insight into each application and can distinguish and offer optimal products for each use case.

Let’s Start Something new
Say Hello!
Project Coordinator
Dr. Jonas Groten
Joanneum Research (Austria)
symphony@joanneum.at
————————————————–
Dissemination Manager
Michèle Isopp
Messfeld GmbH (Austria)
symphony@joanneum.at